22 Nov 2012
by CGT - 0-Impact Guitars
in Botique Guitar, Custom Guitars, Guitar, Music, Musical Instruments
Tags: botique guitars, casper guitar technologies, CGT, custom guitars, elite guitars, guitar builders, guitar shop, Private Stock
Several weeks ago, I started on a new bridge for a Jazzmaster style guitar that was posted here on my shop blog. The tremolo was dis-assembled and modified. The top portion has now been shipped off to my custom chrome shop for some special work since this guitar is to be in my Elite / Artist Series. I usually put a bit of extra extravagant work into them such as engraving or exotic woods or inlay work.
Several years ago, I discovered a few tricks that could be used to stabilize the tuning on our beloved Jazzmasters. The use of a Mastery Bridge is the biggest part of that upgrade. I really love the thought that went into these bridges and they solve the issues with string angle and the interference with the intonation adjustments brilliantly. They have really taken the compensated saddle concept to a new level of effectiveness.
The #122 – A Private Stock version of my JM Series.
- 1-piece FSC Certified Alder Body
- Custom Sea Foam Green Nitro Lacquer Finish
- Custom AAA+ Grade Curly Maple Neck with the CGT “V” Contour
- Rosewood Fingerboard with Hand Inlay design to be determined
- The CGT Modified Tremolo with a Mastery Compensated Jazzmaster Bridge
- Porter Pickups Custom hand wound P-90’s to my specs – TBD
- Antique White Pearloid Pickguard with a modified lower bout (control section) containing custom engraving and chrome
- Standard Switching and blending using CTS and Switchcraft components
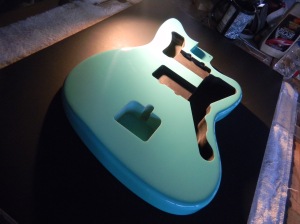
As this project progresses, I’ll post updates. If you have any questions about this project or any other CGT project, please visit me here-
//
22 Nov 2012
by CGT - 0-Impact Guitars
in Botique Guitar, Custom Guitars, Guitar, Music, Musical Instruments, showcar, Uncategorized
Tags: boutique guitars, Casper, casper guitar technologies, custom cars, custom engraving, custom guitars, Electric Guitars, Guitars, guitars and cars, Ibanez, JEM, Sublime
Over the past several weeks, I’ve been posting some bits and pieces of a project I have been working on for a repeat client in Canada. The project has been one that I have enjoyed doing since there was so much additional detail added to the project it took on a very interesting character. There will be additional reviews of this guitar on several of the online forums in the near future, I just wanted to lay out the specs for this guitar as it was built for my client. I’ll leave the grading to him-
One piece Honduran Mahogany Custom Shaped and Contoured JEM AANJ Style Body
Custom Handcrafted Poly Showcar Finish applied by the World Class Showcar Company R.I.P.C.C.

A 3-Piece Maple / Ebony Custom Profiled neck with a custom 13-degree angle peghead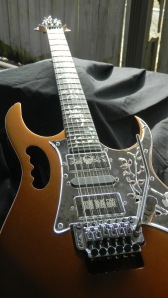
Custom extra fancy mother of pearl Vine of Life inlay
Custom hand-wound Sublime Pickups out of Hungary
A customized Schaller 2-Post tremolo System with enhanced bell brass block
Custom Silver Tuners and Knobs (to be applied by my client upon delivery)
SNAGG RFID Theft Deterrent System Custom Installation in a discreet location on the body
Custom Acrylic Mirror Pickguard – Axtreem Creation
Custom Steel, Engraved / Chrome Tremolo Cover and Truss Rod Cover Plates – Eddies Hand Engraving

The weight on the completed project is 10.8 Lbs
Neck Contour – Wiz Thin (22.5mm @1st Fret – 27.0mm@ the 12th fret)
Fingerboard Radius – Compound 14″ – 16″
Scale Length – 25.5″
Frets – 24 Stainless Steel Frets – (Jameco – 5100S)
Gotho 510 Delta Series Tuners – 4X2 configuration
Special Notes –
My client has asked that there be an additional coat of clear applied to the finish for added depth. There has also been a modification to the tremolo arm (not shown) where I am using an off brand style for the appearance the client has requested. I added an insert to the original location, drilled it out to match the new arm and tapped a thread into the insert. This system is then inserted into the original location and secured with the original mounting overcap.
For more information on this or any of my guitars, visit me HERE-
12 Nov 2012
by CGT - 0-Impact Guitars
in Botique Guitar, Custom Guitars, Guitar, Music, Musical Instruments, Uncategorized
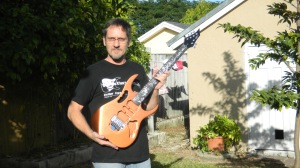
Holding the BDJEM3 after setting the neck and installing the “Ghost Ground” System
I was doing the build up on a project that I’ve been working on getting all the pieces ready for a final assembly day. Well, that day was here. So I wanted to get a few shots of a technique I use to install a string ground from the control cavity to the bridge pivot stud or post that I call, The “Ghost” Ground. get it, Casper the Ghost-
There is no real trick, just a cool way to run the wire and not have to run it thru the tremolo cavity.
1 – Select the route your wire will take. Thru the control cavity, thru the pickup cavity. In the case of the BDJEM3 I’m using for this example, I’ll be running the wire thru the control cavity to the bridge stud hole.
2 – Drill a small hole into the stud hole. Hint – use a long bit 12″ or so to get the steep angle needed to hit the post hole correctly.
3 – Insert a ground wire into the hole from the cavity to the stud hole. make sure you strip the insulation from the end of the wire that will make contact with the stud.
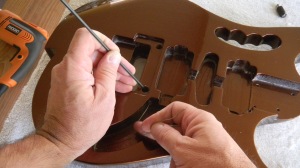
Ground wire placed into the stud / post hole thru the control cavity
4 – Insert the stud and using a block, tap the stud into the hole until it seats firmly on the bottom of the hole.
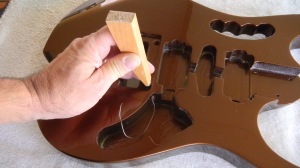
Using a block to tap the stud into position
Route your wire thru the control cavity to the location it will terminate and your all done.
If you wish to completely conceal the wire, this step can be performed prior to applying a finish and the wire all but vanishes.
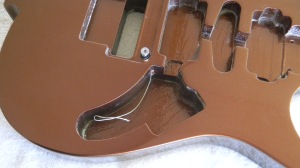
I’ve almost completed this build and will be performing some detailed setup fret work over the next few days. Once all is completed, I’ll be posting the completed project. If you arr interested in more information, check out www.Casper-GT.com
Stay Tuned!
08 Oct 2012
by CGT - 0-Impact Guitars
in Botique Guitar, Custom Guitars, Guitar, Musical Instruments
Tags: boutique guitars, casper guitar technologies, CGT, dna, elite guitars, engraver, inlay technique, JEM inlay, Private Stock, vai
As a fan of the JEM’s for years, I decided to build one for my private collection but I wanted to do something not too flashy but unique. That’s why I decided on an EVO / DNA style with some of my own enhancements.
You have seen the custom JEM Tribute I’m currently working on for a client. This project is very different in it’s design.
The body is a 3-piece basswood. This design keeps the neck, pickups and bridge on the same section of the body enhancing the energy transfer.
I use the Schaller Locking Tremolo system with a custom enhanced bell brass block for enhanced sustain and overall tone upgrade-
I’ve not completely decided on the pickups as of yet. I have the custom project in the works now that has a set of custom wound Sublime Pickups. Once I get to play them, I’ll make a decision as to the possible use of them.
I really liked the DNA inlay so that was a must as well as the white finish. But the EVO was beat
up pretty good, so I wanted it to be like a new version. How it would have looked fresh. So I enlisted the help of my friends at RIPCC again for this project to produce the Diamond White finish.
Like the other project, I’ll be making some custom engraved plates. They are at the engraver now being polished and the design laid out.
04 Oct 2012
by CGT - 0-Impact Guitars
in Botique Guitar, Custom Guitars, Guitar, Musical Instruments
Tags: boutique guitars, casper guitar technologies, CGT, custom guitar, elite guitars, JEM, JEM inlay, tree of life, truss rod
With the body back from the painter, I am able to perform the final fitting of the neck and finalize the size and shape / contour prior to applying the finish to the completed neck. Since most of the milling has been complete and the material has had a chance to settle, it’s time for the sealing and finish coats. The settling process is very important due to the small changes the wood goes thru due to the stress and heat / friction of the shaping process. Larger companies have many necks setting there for days adjusting and acclamation so there are no delays. With a small custom shop, there must still be the wait for the settling. If not, there are shifting and cracking possibilities.
Once the neck is dry, I’ll pack it up and ship it off to Las Vegas to the RIPCC Contractor. They will apply the final coats of sealing and then do the custom color to match the completed body. I’m using the same artist as with the body to avoid having to re-explain the entire concept. I’ve already been thru the planing and design on this project with this artist.
I’ve also heard back from my engraver and he has sent me a photo of the first look at the Vai logo engraving on the truss rod cover plate I made a few days ago. This will be polished a bit more as well as having the outline sharpened. I’ve made several custom covers over the past several months for many styles of guitar. If you have an part you can’t seem to find or you want something special / unique, let me know. CLICK HERE!
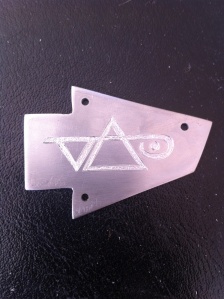
Both items will be heading to Vegas in the next day or so to be painted / chrome plated and returned to me for assembly in the next week. Over the next few days, I’ll be preparing the body for the bridge installation and will install all the electronics into the pick-guard as well.
02 Oct 2012
by CGT - 0-Impact Guitars
in Botique Guitar, Custom Guitars, Guitar, Music, Musical Instruments, Uncategorized
Tags: botique guitars, boutique guitars, casper guitar technologies, custom guitar, custom guitars, elite guitars, guitar builders, Private Stock, tree of life, vine inlay
I have a client I did a previous Curbow completion project for that has asked me to complete yet another body for him.
This time, it’s a purple-heart body. Same shape and same contour / thickness as the last project.
This time, he has given only minor specifics as to the use and playability of this instrument and has given me full control of the design and performance aspects of this build.
He has asked me to select and design an inlay pattern for it as well as select the pickup / electronics. I will be using a vine / tree of life inlay pattern using a variety of pearl. Abalone and MOP will be the most likely material.
I have also selected a beautiful piece of Birdseye Maple for the neck. This with a dark Ebony fingerboard with some subtle inlay work will cap off this new custom Curbow Completion creation.
- 25-1/2″ Scale
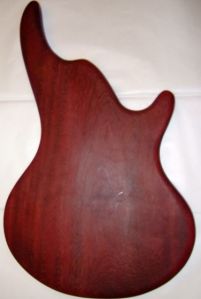
- Purple-heart Custom Curbow Body
- Birdseye Maple neck-wood
- Ebony Fingerboard with custom vine/tree of life hand inlay work
- Gold Gotoh 510 Tuners
- Gold Gotoh Wrap Bridge
- Pickups and electronics to be determined
As this project evolves, I’ll make post here. I hope to have this project completed by Thanksgiving.
02 Oct 2012
by CGT - 0-Impact Guitars
in Botique Guitar, Custom Guitars, Guitar, Music, Musical Instruments, Uncategorized
Tags: boutique guitars, casper guitar technologies, custom guitars, elite guitars, guitar shop, JEM, JEM inlay, pearl inlay, Private Stock, vine inlay
In the operation of my shop, I sometimes use some unusual and special craftsmen to help me complete special projects. This week was no different. I had a need for some special paint color matching and effect work to be done on a JEM tribute project I’m working on. (there have been other posts referencing the same project)
What I’ve done is combine new age guitar design with vintage materials and a custom show car company for paint, engraving and chrome. My friends at RIPCC in Miami have been a fantastic resource for color and finish options on my custom projects. RIPCC have been featured in several Low-Rider magazines as well as won many shows and competitions around the US.
This project is really progressing well. One of the first of this style guitar I’ve done. I love this style. I building one of my own for my Private Stock Collection. Want to learn more? Click Here-
The other day, I received the body back from the painter. Here is a quick shot with some of the parts placed into respective orientation for concept purpose.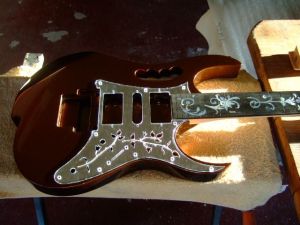
As I progress with this project, I’ll post additional information and photos.
Here are some shots of the Sublime Pickups the client had custom wound for this project.

Sublime Pickups come from Hungary. This project truly has become an International Project.
19 Sep 2012
by CGT - 0-Impact Guitars
in Botique Guitar, Custom Guitars, Guitar, Musical Instruments, Uncategorized
Tags: botique guitars, casper guitar technologies, CGT, custom guitar, elite guitars, engraver, guitar builders, guitar shop, Private Stock, truss rod
So, I’m working with a client that has me commissioning a JEM style guitar for him. He has a thread on a lot of the guitar online forum’s so he likes to post updates to his build every once in a while.
So the latest item I did was produce a truss rod cover to be engraved and chrome plated to match the other hardware on the project.
I was not able to locate a blank metal plate matching my specs so the next thing to do is fabricate one. I purchased a piece of 16 gauge steel at my local hardware store and marked out the exact style cover I wanted for this project. Since my peg head slopes differently than the standard JEM, I opted for an alternative style cover.
After the rough cut on the band saw, the edges need to be squared up and rounded / polished to some degree. This is done by hand as is most detail operations in my shop.
Once squared up, I’ll polish the plate so my engraver can do his work. The next step will be off to Vegas for the expert chrome application and polish. This plate is one of 2 plates I’m making for two separate guitars in progress right now. Looking for a custom or hard to find part? Look no more, I’ll make it. Drop me a line-
18 Sep 2012
by CGT - 0-Impact Guitars
in Botique Guitar, Custom Guitars, Guitar, Music, Musical Instruments, Uncategorized
Tags: Jazzmaster, Private Stock
The other day I was working on my Private Stock Jazz-Master and decided to show one or two of the mods / upgrades I perform to enhance the playability of the traditional offset.
The first thing I do is never use a stock Jazz Bridge.
I get a Mastery Bridge and use them as well as their thimbles. Best in the world in my opinion. As I build this project out, I’ll take some shots of the bridge but for now, just a shot of it on the bench-
The next thing is to acquire a tremolo assembly for the project. I selected a standard Jazz-master trem from one of my regional suppliers. I then disassemble the entire assembly.
I replace the support block or bottom mass plate, with a thicker and a bit more rounded edge plate made of brass. This really enhances the overall tone and clarity of the guitar. This functions pretty much the same as replacing the tremolo block on a Floyd Rose or similar locking system.
Another adjustment / mod I perform is to round off the edge of the string plate alignment support. This allows there to be more of a fulcrum at that point to allow smoother tremolo action. This also improves tuning stability as it reduces the amount of squared edge to stop the return of the string plate to it’s intonated position.
Those are just a few of the mods I perform on most private stock instruments as well as some of the custom guitars I build.
12 Sep 2012
by CGT - 0-Impact Guitars
in Botique Guitar, Custom Guitars, Guitar, Music, Musical Instruments, Uncategorized
Hi There – Another crazy day here in the shop. Trying to plan out how I’m going to work out a meeting schedule for today so I figured this was a good thing to write about in the shop blog.
The first item up is to plan out a meeting with a repeat client. He has a few partial guitars he wants to complete and try to sell in his shop. They are old Jackson DINKY’s that he would like to transform into a couple of old relic road dogs. But, he doesn’t want to put much into them. Just so happens, I have a very good supply of old parts lying around so I should be able to get him something going pretty easily and cost effective. Nicely worn Tremolo, some old effective tuners and some fresh pups. He is a great client and has been a good customer of mine for a few years now. I’ll do my best as usual to give him a great price
Next up is a meeting with my long time client / repeat customer I’ll refer to as JT- I have his Curbow Completion project he will get to play for the first time today. This meeting is at his studio fairly close to my shop so this should not be too much of a problem getting to. JT and I will also be developing the next project to be started, the Purpleheart Curbow Project. We will be reviewing JT’s vision then plan the project. These projects usually require a bit of engineering so the cost tends to fluctuate a bit. Having a client that trusts you makes these projects go so much better. These projects aren’t the recommended type for new customers unless you are extremely established in your area. That trust is something that has to be earned
Next is a new client that was referred to me by another shop I do work / custom mod’s with here in Miami. He has several parts he purchased from around the world that are suppose to be a tribute version of a early model JEM. Problem is the neck pocket is not correct for the AAJN neck (body was made in Brazil). Thus requiring a new neck joint route or an adjustment to the existing pocket. A review of the project scope as well as a quote for the project will be required.
The last two on this list are easily completed together. I’ll contact my clients and have them meet me at the studio. The 2 builds are from a shop not very close to me. So what I think I’ll do is go see my engraver to drop off a future project, stop by another supply house here then meet with my new client.
This is a typical day here at CGT along with the other normal day to day activities. There will always be a need to manage your time. The better you get at that, the better your chances for success in the long run-
Previous Older Entries