07 Apr 2013
by CGT - 0-Impact Guitars
in boutique guitars, Custom Finish Options, Custom Guitars, Guitar, handmade guitars, Music, Musical Instruments, Uncategorized
Tags: boutique guitars, casper guitar technologies, custom guitars, elite guitars, guitar builders, guitar shop, Private Stock, Sublime, tree of life
So I’ve been hearing about this new method of drying lumber that is alleged to correct some stability issues. The wood in
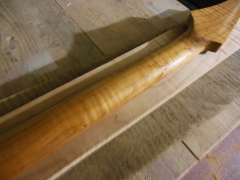
Interesting flame figure-
question is maple. Seems to be most varieties tend to shrink and expand with heat, moisture / humidity and altitude (minute but existent). This causes in the most extreme cases, intonation problems until stable. Cracking finish and even cracked neck.
Now, I’ve been playing guitar for over 40 years. I’ve lived in Ohio, Korea, Germany, Alabama, Mississippi & South Florida. I’ve also traveled all over Europe with a few guitars and I can say the phenomenon is real. I have a guitar I built back in 1985 and a Steinburger (Factory Mod GP2T) The graphite neck seems to be the most stable as far as tuning / intonation goes. I’ve never seen either one of those guitars cause any problems with the neck joint or expansion around the tuners or other hardware.
So Like I said at the start, I heard about this Roasting technique and was naturally intrigued. I read up a bit on the process and benefits and agree for the most part with the theory. Like I said, I have seen some of the location / environment effects on guitars. I would like to see if this innovation is worth the effort.
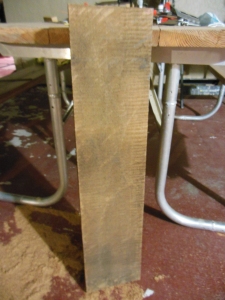
as shipped roasted maple stock-
First off, the material is not the easiest to track down. Not as many people producing it as you would think. But those that do, are quite proud of their processes. I won’t mention any here. do a simple search to generate a good list to start with if you are interested in acquiring a piece to try out. If not, leave it to your builder to get if you wish to test out the material after this-
I purchased about 10 feet. Had it cut into 36″ chunks for shipping. When it arrived, it smelled like a camp fire. (Good in my book, if you don’t like the smell of a fire out by the camp then this isn’t your wood). This smell is even more present when you start to work with the wood. I enjoyed working this material.
Since the process drives virtually all of the moisture out of the wood, it does seem to tare just a bit. Not horrible but you must control your tools and remove very little amounts during the contouring phase as well as the filing-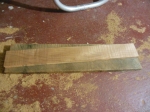
Over all, the board worked well for this application. I will be continuing this build as well as testing by shipping it overseas as well as around the US for climate test / stability.
If you would like more information on this or any other Casper Guitar Technologies project, click HERE-
//
26 Feb 2013
by CGT - 0-Impact Guitars
in boutique guitars, Custom Guitars, Guitar, handmade guitars, Music, Musical Instruments, Uncategorized
A few post’s back, I wrote about the modifications I do to a Jazzmaster Tremolo to enhance the experience with the boutique bridge from Mastery and the likes.
What I do is increase the mass of the tremolo by adding a brass plate to the tremolo, replacing the weak plate that comes
with the tremolo standard.The standard plate weighs about 30 grams where my plate weighs in at almost 70 grams.
What I source is a nice brass plate from the same metallurgist shop that produces the bell brass used by high end chimes and bell manufacturers. I have found over the years that this really improves the response of the guitar and increases the sensitivity and accuracy of the bridge.
The plan is to have this assembly installed into my Jazzmaster with a set of custom P-90s in the next few weeks. As soon as I do, there will be some files posted.
03 Feb 2013
by CGT - 0-Impact Guitars
in boutique guitars, Custom Guitars, handmade guitars, Music, Musical Instruments, Uncategorized
Tags: boutique guitars, casper guitar technologies, CGT, custom guitar, custom guitars, Electric Guitars, elite guitars, guitar builders, guitar shop, guitars and cars, Private Stock
Tremolo’s come in a variety of flavors as one would expect in the world of guitars. But when it comes to locking tremolos, I like to use the Schaller Version. They are made under the same license / concept as the Floyd Rose and are made by the same company in Germany that made the original Floyd.
Many years ago, I discovered that the tremolos that had some weight to them really had a hands down tone advantage over the lighter weight varieties. So in pursuit of that tone, I began to experiment with various materials that would increase the mass at the block and eventually landed upon Bell Brass. It’s resonant characteristics as well as it’s increased density create the mass I was looking for in the correct size as well. Brass is an easy material to mill as well so it adds to it’s usefulness in my shop of limited metal working capabilities.
To procure a block, there are several manufacturers of these blocks out there. Just do a search on the internet and find the flavor of your choice. I use a shorter block due the the fact I recess the tremolo’s on most of my projects. The shorter block is required due to the depth of the block. If you use the standard 42mm block, it will normally protrude out the back of the guitar causing stability issues while being played as well as hanging up on your outfit / clothes during playing.
When you get your block, remove the saddles from your bridge being careful to maintain their order. Most versions have some radius and mixing these up can cause issues with proper string height and radius.
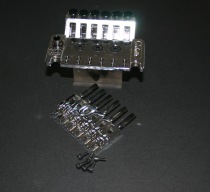
Next, remove the 3 block screws. Be careful to maintain control of the block and bridge. There are 2 plates between the block and the bridge base plate. Be sure to maintain the orientation of these plates. They have a purpose and must be placed back in the same position.
The block may have a specific orientation as well. be sure you evaluate your block to be sure it is being placed onto the base properly. Using the screws that came with your block, secure the parts together and tighten the screws pretty snug.
Replace the saddles in the proper orientation and secure the saddle screws. Your now ready to install the bridge into your guitar. Set your height, string it as normal and play. You’ll notice a bit more punch, more bite and sustain that may last for days. This in one of the single most dramatic upgrades you can do to your guitar that doesn’t involve solder. It is fairly simple to perform but may prove to be a bit too daunting for the novice. If you doubt your DIY capabilities, your local shop should be able to help you out.
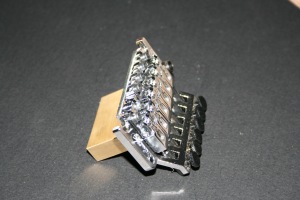
To see this in action, click HERE
27 Dec 2012
by CGT - 0-Impact Guitars
in boutique guitars, Custom Guitars, Guitar, Music, Musical Instruments, Uncategorized
Tags: boutique guitars, casper guitar technologies, custom guitar, custom guitars, Electric Guitars, elite guitars, guitar builders, guitar shop, JEM, Private Stock, Sublime, tree of life
As you know, last month, I completed the build of a JEM Tribute guitar for one of my long time clients in Canada. He usually does reviews of his projects on the forums and blogs etc. Since he does these reviews, he likes to
use companies he hasn’t used in the past so he can get new vendors and companies a bit of press and exposure. One of the companies he used, and subsequently introduced me to was Sublime Pickups out of Hungary. (Sublime Pickups) once the page opens, click on the button with “Bezar”
After being introduced, I received a set of pickups from my new friend Andras for my clients guitar. I immediately discovered these pickups were not your usual breed of pickup. They were pretty hefty and seemed to be pretty well made and solid. Nice polish to the chrome covers and the engraving was very eloquent. Once installed, it became evident these were not your normal pickups. Very cool tone and some features I like to see in my select builds such as nice volume response, concice and clear note separation, some very cool natural distortion and a subtle ring (like a bell ringing the exact note being played) by design to offset the note of the wood (mahogany body).
Once I completed the project, I delivered it to my client and he is still playing around with it. Testing out all the versatility of the guitar and it’s ability to adapt to many playing styles. Once the review is published, it will be noted here in my blog.
But that isn’t where this story ends-
After a few weeks, I was contacted by Andras, the creator of the pickups. He let me know that there were a few sets in the US that were stranded at a test facility that was no longer able to conduct his testing and he would like to know if I would like to receive them and conduct the testing for him as well as complete the shipping process on an additional set for an artist located here in the States. I naturally accepted and have since received the pickups.
So given the fact that these pickups really set off a fire storm with the JEM build, I’ve decided to build another private stock variation of the JEM I did last month. This version will be built based on a 2 – piece alder body finished in either a translucent black or a black metallic finish. A rock maple neck with an ebony fingerboard and Red Inlay to match the pickups I received, stainless steel 5100 frets. In addition, the version I build will have the “Grip” but it will not have a Center Pickup. So basically it will be an RG of some sort with rear routing and mounting rings. I’ll add a variety of switching options since the pickups have been setup for just that option. As a mater of fact, the neck pickup has been designed specifically for the coil tap option to reduce the output on demand.
Just a bit of detail on the pickups:
- Style – Red Resin Cast Humbucker with custom artwork engraved – (that’s a whale on the bridge pickup, the neck graphics are pretty self explanatory I think)
- Neck – Distant Land with DCT 17.2k / 9.3k
- Bridge – Deep Ocean Blue – 19.8k
Once again, the bridge of choice in my shop is the CGT Modified Schaller Double Locking (Floyd Rose License) with the shortened, increased mass brass block will be used on this project as well as the Schaller Staggered / locking tuners, all chrome-
For additional information on this or any other CGT projects, click HERE–
20 Dec 2012
by CGT - 0-Impact Guitars
in boutique guitars, Custom Guitars, Guitar, Musical Instruments, Uncategorized
Tags: boutique guitars, casper guitar technologies, CGT, curbow, custom guitars, Electric Guitars, elite guitars, guitar builders, guitar shop, guitars and cars, inlay technique, pearl inlay, Private Stock, vine inlay
Over the last few days, I’ve been working on the completion of the contour of the neck back. What I’ve got for now is a pretty thick neck. .85″ at the 1st Fret and about .95″ at the 12th. Once again, it’s a 24 fret, 25.5″ scale Ebony with a modified Vine of Life Inlay on a beautiful AAAA grade Birdseye maple neck with a Hot-Rod Double action truss rod.
I used a large poster board with graph lines and a Drafting “T” to determine the center-line on this guitar. By centering the body on the graph, you are easily able to mark and apply the center-line onto the body. This line will be used for all routs as well as the bridge alignment and strap locks.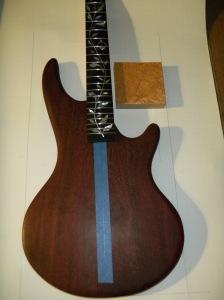
The neck-joint was routed to a depth of .725″ to allow for the string to body height my client is requesting. This is then supplemented with a thin sanding screen to help the neck grip well to the epoxy coating these bodies have as the laminated material separating the top half and the bottom half of the guitar body.
Next up will be the Bridge placement as well as the pickup and control cavity routing.
10 Dec 2012
by CGT - 0-Impact Guitars
in boutique guitars, Custom Guitars, Guitar, Music, Musical Instruments, showcar, Uncategorized
Tags: boutique guitars, casper guitar technologies, CGT, custom guitar, custom guitars, elite guitars, guitar builders, guitar shop, JEM, JEM inlay, Private Stock, vine inlay
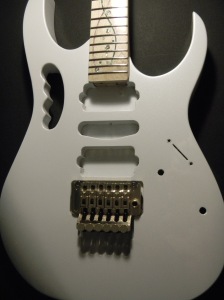
Blonde DNA Custom EVO
Since the last update on this project, there have been several developments. I’ve received the EVO 2 and Evolution pickups and have installed the Tremolo system. I’ve created a typical CGT system as I’ve used in the past.
A Floyd / Style trem with a R2 locking nut. Since the hardware is Gold, I’ve taken
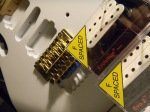
Dimarzio EVO-2 and Evolution neck for this project.
part of a chrome nut and placed gold locking blocks to give it a custom look. I think it works and since I had the parts here in the shop I figured why not use them.
I’ve also completed the finish on the peg-head. I applied a polar white color with clear overcoat. I’ve also installed the water-slide logo.
The electronics will be a 5-way super switch giving me a pretty wide range of pickup combinations, a set of CTS solid shaft pots with an orange drop .047uf tone cap.
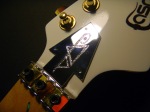
VAI Custom Engraved Plate
Like so many projects before, I’ve used my friends at RIPCC for the beautiful Diamond White Metallic finish on this project. I love what they bring to the project. Combining show-car aspects with the modern edge of the electric guitar. Really a natural combination in my opinion. My friend Eddie at Eddies Hand Engraving lent his skills on the Truss Rod cover for this tribute axe as well.
22 Nov 2012
by CGT - 0-Impact Guitars
in Botique Guitar, Custom Guitars, Guitar, Music, Musical Instruments, showcar, Uncategorized
Tags: boutique guitars, Casper, casper guitar technologies, custom cars, custom engraving, custom guitars, Electric Guitars, Guitars, guitars and cars, Ibanez, JEM, Sublime
Over the past several weeks, I’ve been posting some bits and pieces of a project I have been working on for a repeat client in Canada. The project has been one that I have enjoyed doing since there was so much additional detail added to the project it took on a very interesting character. There will be additional reviews of this guitar on several of the online forums in the near future, I just wanted to lay out the specs for this guitar as it was built for my client. I’ll leave the grading to him-
One piece Honduran Mahogany Custom Shaped and Contoured JEM AANJ Style Body
Custom Handcrafted Poly Showcar Finish applied by the World Class Showcar Company R.I.P.C.C.

A 3-Piece Maple / Ebony Custom Profiled neck with a custom 13-degree angle peghead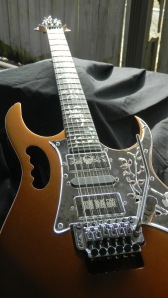
Custom extra fancy mother of pearl Vine of Life inlay
Custom hand-wound Sublime Pickups out of Hungary
A customized Schaller 2-Post tremolo System with enhanced bell brass block
Custom Silver Tuners and Knobs (to be applied by my client upon delivery)
SNAGG RFID Theft Deterrent System Custom Installation in a discreet location on the body
Custom Acrylic Mirror Pickguard – Axtreem Creation
Custom Steel, Engraved / Chrome Tremolo Cover and Truss Rod Cover Plates – Eddies Hand Engraving

The weight on the completed project is 10.8 Lbs
Neck Contour – Wiz Thin (22.5mm @1st Fret – 27.0mm@ the 12th fret)
Fingerboard Radius – Compound 14″ – 16″
Scale Length – 25.5″
Frets – 24 Stainless Steel Frets – (Jameco – 5100S)
Gotho 510 Delta Series Tuners – 4X2 configuration
Special Notes –
My client has asked that there be an additional coat of clear applied to the finish for added depth. There has also been a modification to the tremolo arm (not shown) where I am using an off brand style for the appearance the client has requested. I added an insert to the original location, drilled it out to match the new arm and tapped a thread into the insert. This system is then inserted into the original location and secured with the original mounting overcap.
For more information on this or any of my guitars, visit me HERE-
12 Nov 2012
by CGT - 0-Impact Guitars
in Botique Guitar, Custom Guitars, Guitar, Music, Musical Instruments, Uncategorized
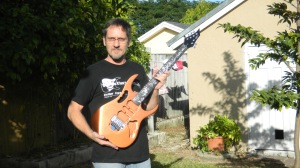
Holding the BDJEM3 after setting the neck and installing the “Ghost Ground” System
I was doing the build up on a project that I’ve been working on getting all the pieces ready for a final assembly day. Well, that day was here. So I wanted to get a few shots of a technique I use to install a string ground from the control cavity to the bridge pivot stud or post that I call, The “Ghost” Ground. get it, Casper the Ghost-
There is no real trick, just a cool way to run the wire and not have to run it thru the tremolo cavity.
1 – Select the route your wire will take. Thru the control cavity, thru the pickup cavity. In the case of the BDJEM3 I’m using for this example, I’ll be running the wire thru the control cavity to the bridge stud hole.
2 – Drill a small hole into the stud hole. Hint – use a long bit 12″ or so to get the steep angle needed to hit the post hole correctly.
3 – Insert a ground wire into the hole from the cavity to the stud hole. make sure you strip the insulation from the end of the wire that will make contact with the stud.
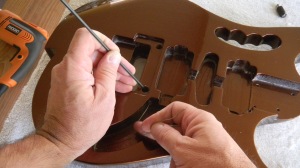
Ground wire placed into the stud / post hole thru the control cavity
4 – Insert the stud and using a block, tap the stud into the hole until it seats firmly on the bottom of the hole.
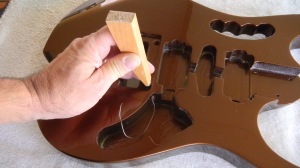
Using a block to tap the stud into position
Route your wire thru the control cavity to the location it will terminate and your all done.
If you wish to completely conceal the wire, this step can be performed prior to applying a finish and the wire all but vanishes.
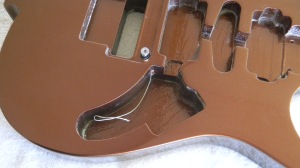
I’ve almost completed this build and will be performing some detailed setup fret work over the next few days. Once all is completed, I’ll be posting the completed project. If you arr interested in more information, check out www.Casper-GT.com
Stay Tuned!
Previous Older Entries